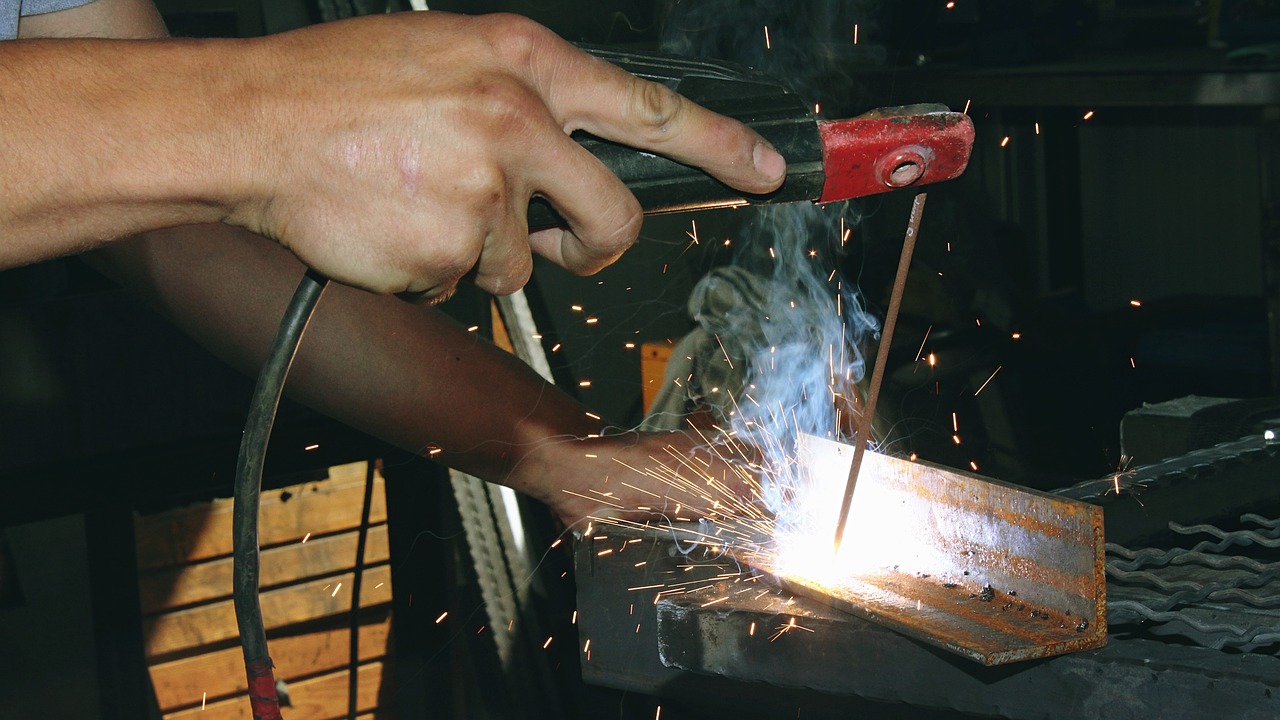
Frezowanie elektrod jest kluczowym procesem w przemyśle zgrzewarek, który zapewnia precyzyjną obróbkę materiałów, niezbędną do uzyskania wysokiej jakości połączeń zgrzewanych. Elektrody są podstawowym elementem w zgrzewaniu, odpowiadającym za przewodzenie prądu i generowanie ciepła potrzebnego do połączenia materiałów. Aby zapewnić ich długowieczność oraz skuteczność, niezbędne jest stosowanie zaawansowanych technik frezowania, które pozwalają na utrzymanie odpowiednich parametrów ich powierzchni roboczych. W artykule omówimy różne techniki frezowania, które znajdują zastosowanie w produkcji i konserwacji elektrod, a także ich znaczenie dla funkcjonowania zgrzewarek.
Rola frezowania w procesie zgrzewania
Frezowanie jest jednym z najważniejszych procesów obróbki mechanicznej stosowanych przy produkcji i regeneracji elektrod. W zgrzewaniu oporowym, gdzie elektrody stykają się bezpośrednio z materiałem, frezowanie odgrywa kluczową rolę w zapewnieniu odpowiedniej geometrii i czystości powierzchni roboczych. Precyzyjna obróbka pozwala na zachowanie odpowiednich parametrów, takich jak płaskość i gładkość, co jest niezbędne do prawidłowego przewodzenia prądu oraz generowania równomiernego ciepła podczas zgrzewania.
Zgrzewanie wymaga, aby elektrody miały idealnie dopasowane powierzchnie robocze, co zapewnia równomierne rozłożenie nacisku i minimalizuje ryzyko powstawania defektów w połączeniach. Właśnie tutaj frezowanie okazuje się nieodzownym elementem, ponieważ umożliwia uzyskanie pożądanych wymiarów i kształtów, co z kolei przekłada się na jakość i trwałość zgrzewanych elementów.
Techniki frezowania elektrod
Frezowanie elektrod można realizować za pomocą różnych technik, z których każda ma swoje specyficzne zalety i zastosowania. Jedną z najczęściej stosowanych metod jest frezowanie konwencjonalne, w którym obrabia się elektrody za pomocą frezów obrotowych, usuwając nadmiar materiału i formując powierzchnię roboczą. Ta technika jest powszechnie stosowana w produkcji elektrod miedzianych, które są szeroko używane w zgrzewarkach oporowych.
Kolejną zaawansowaną techniką jest frezowanie CNC (Computer Numerical Control), które umożliwia precyzyjne sterowanie procesem obróbki dzięki wykorzystaniu komputerowych programów sterujących. Frezowanie CNC pozwala na osiągnięcie bardzo wysokiej dokładności, co jest niezbędne w produkcji elektrod o skomplikowanych kształtach i małych tolerancjach wymiarowych. Dzięki tej technologii możliwe jest także seryjne wytwarzanie identycznych elektrod, co jest szczególnie istotne w produkcji masowej.
Nieco mniej powszechną, ale niezwykle precyzyjną techniką jest frezowanie elektroerozyjne, które polega na kształtowaniu powierzchni elektrody za pomocą iskrzenia elektrycznego. Metoda ta jest stosowana przede wszystkim do obróbki twardych i trudnoskrawalnych materiałów, takich jak wolfram czy molibden, które są używane w elektrodach stosowanych w zgrzewarkach oporowych.
Znaczenie materiałów używanych do produkcji elektrod
Wybór materiału, z którego wykonane są elektrody, ma bezpośredni wpływ na skuteczność i trwałość procesu zgrzewania. Najczęściej stosowane materiały to miedź, stopy miedzi z chromem lub cyrkonem, oraz materiały kompozytowe, takie jak węgliki spiekane. Każdy z tych materiałów charakteryzuje się odmiennymi właściwościami, które determinują sposób obróbki i przeznaczenie elektrod.
Miedź, dzięki swojej wysokiej przewodności elektrycznej i cieplnej, jest idealnym materiałem na elektrody stosowane w zgrzewaniu cienkich blach stalowych i aluminiowych. Stopy miedzi, takie jak CuCrZr, charakteryzują się większą twardością i wytrzymałością mechaniczną, co sprawia, że są one lepszym wyborem w zgrzewaniu materiałów o wyższej twardości lub w procesach wymagających dłuższego czasu zgrzewania.
Materiały kompozytowe, takie jak węgliki spiekane, są stosowane w najbardziej wymagających aplikacjach, gdzie elektrody są narażone na intensywne zużycie mechaniczne oraz wysokie temperatury. Ich twardość i odporność na ścieranie sprawiają, że mogą być używane w zgrzewaniu materiałów o wysokiej wytrzymałości, takich jak stale nierdzewne czy stopy tytanu.
Frezowanie jako metoda regeneracji elektrod
Elektrody zgrzewające, ze względu na intensywne użytkowanie, z czasem ulegają zużyciu, co prowadzi do pogorszenia jakości zgrzewów. Frezowanie stanowi skuteczną metodę regeneracji zużytych elektrod, przywracając im pierwotne właściwości i przedłużając ich żywotność. Regularna konserwacja elektrod poprzez frezowanie pozwala na utrzymanie stabilnych parametrów zgrzewania, co jest kluczowe w produkcji masowej, gdzie niezawodność procesu ma decydujące znaczenie.
Regeneracja elektrod poprzez frezowanie obejmuje usunięcie zużytej warstwy materiału oraz nadanie powierzchni roboczej odpowiedniego kształtu i gładkości. Proces ten pozwala na przywrócenie elektrod do stanu zbliżonego do nowego, co jest nie tylko ekonomicznie opłacalne, ale także ekologiczne, ponieważ zmniejsza ilość odpadów produkcyjnych.
Precyzja i jakość w frezowaniu elektrod
Precyzja obróbki jest jednym z najważniejszych czynników wpływających na jakość elektrod zgrzewających. Niewielkie odchylenia w wymiarach lub chropowatości powierzchni mogą prowadzić do nierównomiernego rozkładu prądu i ciepła podczas zgrzewania, co skutkuje wadliwymi połączeniami. Dlatego też frezowanie elektrod musi być realizowane z najwyższą dokładnością, z uwzględnieniem wszystkich parametrów technicznych, takich jak geometria elektrody, rodzaj materiału, oraz specyfika procesu zgrzewania.
W nowoczesnych zakładach produkcyjnych stosuje się zaawansowane maszyny frezarskie oraz systemy pomiarowe, które pozwalają na kontrolowanie procesu frezowania w czasie rzeczywistym. Dzięki temu możliwe jest osiągnięcie najwyższej jakości elektrod, które zapewniają stabilność procesu zgrzewania i minimalizują ryzyko defektów.
Automatyzacja procesu frezowania elektrod
W dobie Przemysłu 4.0 automatyzacja procesów produkcyjnych odgrywa kluczową rolę w zwiększaniu efektywności i precyzji obróbki. Frezowanie elektrod nie jest wyjątkiem – coraz częściej stosuje się zautomatyzowane systemy frezarskie, które nie tylko skracają czas obróbki, ale także eliminują błędy ludzkie i zapewniają powtarzalność procesu.
Automatyzacja procesu frezowania obejmuje nie tylko same maszyny, ale także oprogramowanie sterujące, które umożliwia programowanie i monitorowanie całego cyklu produkcyjnego. Zintegrowane systemy pomiarowe i czujniki umożliwiają automatyczną korekcję parametrów obróbki, co pozwala na uzyskanie optymalnych wyników przy minimalnym udziale operatora.
Wprowadzenie automatyzacji do procesu frezowania elektrod ma także korzystny wpływ na ekonomikę produkcji. Skrócenie czasu obróbki oraz zmniejszenie ilości odpadów materiałowych prowadzi do obniżenia kosztów produkcji, co jest szczególnie istotne w przypadku produkcji na dużą skalę.
Przyszłość frezowania elektrod i rozwój technologii
Przyszłość frezowania elektrod z pewnością wiąże się z dalszym rozwojem technologii obróbki oraz automatyzacji. W miarę postępującej miniaturyzacji urządzeń oraz wzrostu wymagań dotyczących precyzji i niezawodności zgrzewania, rola precyzyjnej obróbki będzie zyskiwać na znaczeniu. Nowe materiały, takie jak stopy o podwyższonej wytrzymałości oraz kompozyty, będą stawiały przed technologią frezowania kolejne wyzwania, związane z ich obróbką.
Można się spodziewać, że frezowanie elektroerozyjne oraz techniki hybrydowe, łączące różne metody obróbki, będą odgrywać coraz większą rolę w produkcji i regeneracji elektrod. Równocześnie rozwój technologii CNC oraz automatyzacji pozwoli na dalsze zwiększanie precyzji obróbki oraz skrócenie czasu produkcji.
Podsumowanie: Frezowanie elektrod jako kluczowy element zgrzewania
Frezowanie elektrod to nieodłączny element nowoczesnych procesów zgrzewania, który ma bezpośredni wpływ na jakość i trwałość połączeń zgrzewanych. Precyzyjna obróbka elektrod, z wykorzystaniem zaawansowanych technik frezowania, jest niezbędna do zapewnienia stabilności i efektywności procesów zgrzewania w różnych branżach przemysłowych. W miarę rozwoju technologii oraz automatyzacji, frezowanie elektrod będzie odgrywać coraz ważniejszą rolę, przyczyniając się do dalszego doskonalenia procesów produkcyjnych oraz zwiększania konkurencyjności firm na rynku globalnym.